Success Story » Transportation and Logistics
How Deshler Optimizes Partner Resources To Meet Customer Needs.
GTM’s transportation planning and rapid response capabilities help Deshler partners fulfill customer needs, support manufacturing and meet deadlines.
GTM’s transportation planning and rapid response capabilities help Deshler partners fulfill customer needs, support manufacturing and meet deadlines.
Constant Challenges
In manufacturing, time is everything. Even when you have the right materials in place, skilled team members in position, and well-functioning machinery at the ready, unexpected obstacles arise. Progress slows, production lines stop, and shipments are delayed. Cycle losses become money losses with dizzying speed.
Swift Response
At Deshler, Global Transportation Management (GTM) solves these issues for our plants and our customers, often preventing them before they occur. Through its full integration into Deshler partner activities and supply chain, GTM’s global logistics team supports effective planning, monitoring and rapid responses to urgent customer needs.
Planning for the Unexpected
GTM’s customizable services include all aspects of transportation planning, management and execution across land, sea and air and to and from anywhere in the world. Working with proven global partners and its highly-experienced in-house customs brokers, GTM plays a pivotal role in much of Deshler’s operations and integrated, multi-step customer solutions.
Far more involved than moving items from one place to the next, successful modern logistics plans include multiple stops, minute-to-minute transportation updates, built-in flexibility around driver, load and vehicle types, a consistent environmental consciousness, focus on efficiencies of time, fuel and space, constantly shifting international requirements, and rapid global change that has become the norm.
To support its cross-partner process, GTM’s dispatchers employ the company’s dedicated transportation management system to optimize driver and vehicle time. This dependable yet flexible approach helps keep production moving on schedule, whether vendors are shared or far apart, from a single box of tools to a large shipment.
This capability is especially important when high-pressure situations arise, an inevitability in manufacturing, no matter how carefully a company plans ahead. GTM is typically able to expedite shipments across Deshler companies, to other suppliers, even directly to an automaker when needed. Situations can vary from stepping in for an automaker that has taken a stock loss and urgently needs parts to a new program or vehicle launch requiring intensive, up-to-the-deadline support.
Coordination in Motion
GTM’s multi-partner integration also supports Deshler companies’ day-to-day individual operations. For instance, GTM runs at least one truck daily between Amanda Manufacturing’s plants in Eastern Michigan and Southern Ohio, while maintaining availability of additional trucks and vans as needed. Each day, Amanda sends over their shipment plans and GTM brings them to Feblo, also a Deshler company, for inspection and packaging by the next morning.
For example, Amanda Manufacturing Logan ships striker wire and base plates via GTM’s interstate trucking service to Amanda Manufacturing Livonia. The Amanda Livonia team then assembles the strikers on their state-of-the-art rotary tables, with individual steps organized according to numerous part specifications.
After assembly, Amanda Livonia ships the parts, again using GTM coordination and services, to outside vendors. Even though Deshler partners offer a comprehensive array of services and capabilities, they also work with carefully chosen vendors with proven expertise, in painting, heat treating, plating, tumbling, chroming, machining, some welding and tapping for example, for project completion.
When these additional processes are complete, GTM moves them to Feblo International for sorting, custom packaging and warehousing if needed. Parts are then shipped, again via GTM, to partner companies or to end customers.
GTM’s services are also essential for GS3 Global, Deshler’s supply chain leader and bent metal and assembly provider. As most of GS3’s complex assembly work integrates parts from multiple sources, on-time and coordinated delivery is the only way to maintain production levels. GS3 – as well as other Deshler Group companies – also benefits from GTM’s daily scheduled runs between partner companies.
GTM’s planning, staffing and monitoring expertise also work well for other situations Deshler companies encounter, from break-downs and sudden trip interruptions to unexpected parts and other expediting needs.
"Whether we’re fulfilling an urgent need or making everyday operations work more efficiently for our partners, the GTM team plays a key role. Deshler collaborations work smoothly because our people are on top of their game."
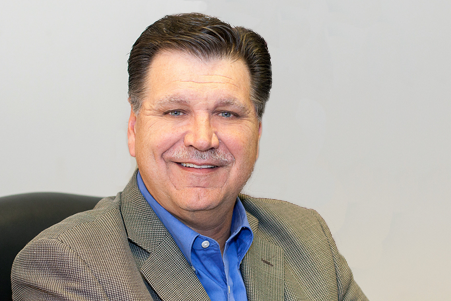
Mark Brodie
Founder, Managing Member and Co-Owner, GTM USA
Conclusion
The beauty of GTM’s service integration across Deshler companies is that it’s often nearly invisible to the end customer, because it’s carefully planned and effective. Deshler customers receive their end products – which have been concepted, manufactured, refined, custom packaged, quality tested, warehoused, shipped – on time and at cost. The many steps involved in that process were coordinated in large part by GTM’s team of logistics planners and transportation specialists.
As Deshler Group’s global business – and the entire transportation industry – continue to evolve, the seamless planning and execution GTM has put in place will propel Deshler’s partners to sustained growth and customer satisfaction.